Evolve For Your Customers
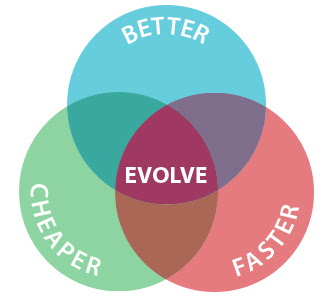
Remember when you could only choose two of the three? Well those days are gone. Today, if you can not deliver on all three you best be looking over your shoulder because someone else will figure out how to do it. It is called evolution.
To stay lean and agile (or effectively evolve) you need to routinely evaluate and invest in your people, facilities, equipment, and most importantly your processes. I’m always amazed at how much wasted time is baked into parts, from setup to inefficient handling, to bottlenecks encountered across the manufacturing process.
At TCI we may take efficiency and quality a little more to heart, because without it we would cease to provide a strong value proposition to our customers. You see, when manufacturers do a self evaluation of their processes and realize how much time is spent just in material preparation, specifically cutting, squaring, and flattening, TCI Precision Metals is usually on the short list of resources to help. Bottom line, we must produce quality precision materials fast, that are ready to go directly from receiving to finished machining, and do it at a net prepared materials cost that is less than the manufacturer can do it themselves. Only then do we have something truly special to offer.
Some of our best internal improvements are recommendations from our employees. It makes sense, especially in our highly specialized business that survives on consistently delivering tight tolerances. Our machine operators are part artisan, part technician, and our investments in equipment and facilities are designed to support them. Terms often applied to how we work include things like grinding, milling, flattening, cutting, etc. And yes, this is somewhat accurate, but there is nothing normal about the equipment we invest in. Virtually every piece of equipment in our 105,000 sq ft facility has been optimized to volume prep materials, including aluminum, stainless steel, titanium, cooper, and more. We prep precision materials far more efficiently than our customers can in their own shop.
In order to maintain a performance edge for our customers we continue to add optimized equipment to the floor. In the last few years alone we have installed two new waterjet cutting machines, state-of-the-art precision sawing, and multiple duplex milling machines, all designed to increase throughput of machine-ready blanks without sacrificing precision.
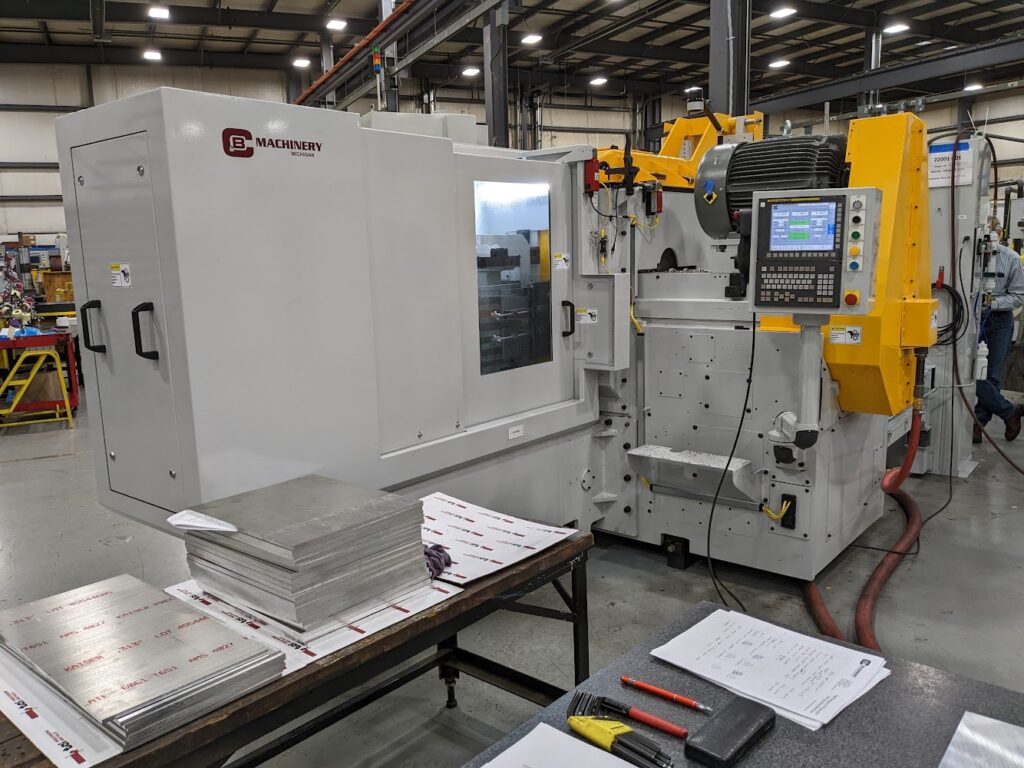
Just recently we added a new take on the age old method of double disc-grinding; a new 42” CNC double-disc grinding center. The process of double-disc grinding removes material equally from both sides of a part at the same time. In the hands of an artisan operator these machines turn-out materials that are flat, parallel, and resistant to movement during finished machining, as inherent material stresses are released during the process. Our new CNC double-disc grinding machine works much the same way, but technology advancements built into the new machine improve our own overall efficiency greatly , compared to traditional double-disc grinders, which will help us shorten customer lead times.
Everyone’s business is different, unique, but the hard work and investment that goes into delivering products and services that are better, faster, and more affordable applies to all. We all need to take the time necessary to evaluate, improve, and execute. Failure to do so is a failure to evolve.
Thanks for reading-
Ben