Materials Machine-Ready for Production (MRP)
Save Time – Improve Quality – Increase Overall Throughput
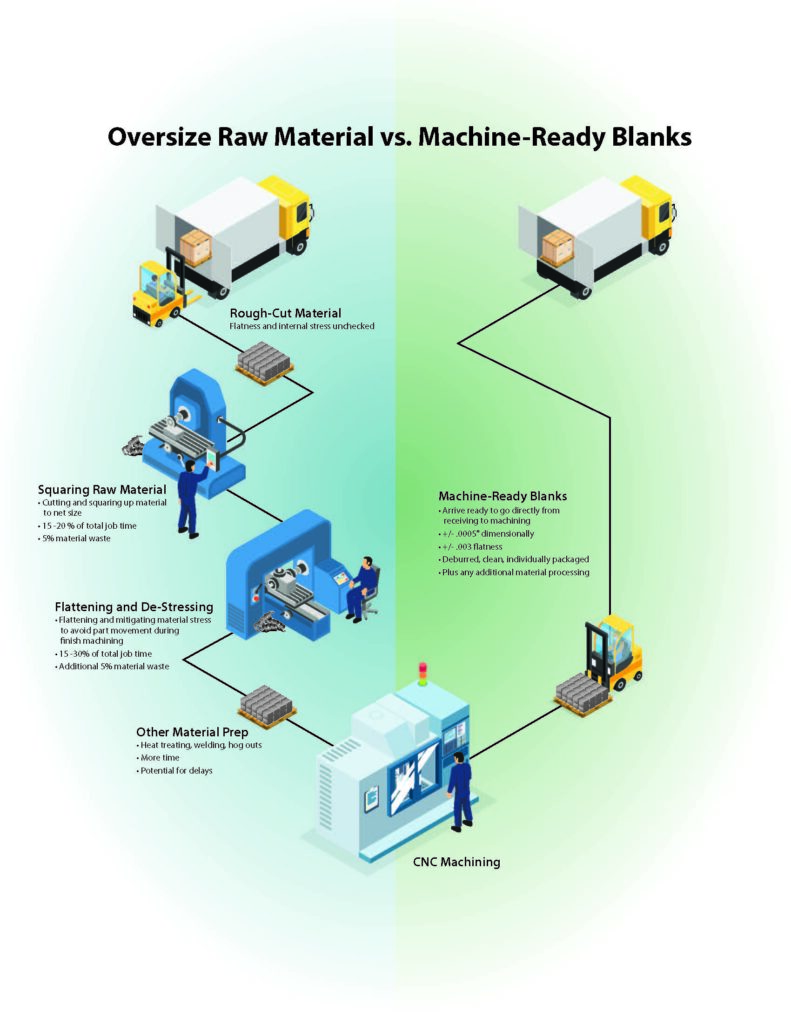
In today’s rapidly evolving manufacturing environment it is important for shops to stay current with best practices while keeping a watchful eye on increasing customer demands. Shops that continue to innovate, retool, and exceed customer expectations are thriving, while at the same time educating customers as to what is possible. Quality, sustainability, reporting, and the environment, as it relates to manufacturing, have never been more scrutinized. How can we do more with less? How can we reduce waste? How can we increase quality? How can we shorten lead times? How can we increase the bottom line? These important discussions are happening in shops everywhere. Working harder is not the answer, you need to think differently. Listen to your customers and challenge the status quo. If you think differently, you will be different, compared to your competition.
Most shops have different production process needs based on their unique workflow, but there are common denominators, for example, materials handling and processing. If you review the most recent value stream mapping of your manufacturing processes you will likely see several steps dedicated to material sourcing, logistics, processing, and prep for finish machining or assembly. There is probably little argument internally about these process steps being required, and completed in-house, even though they can account for more than 50% of the total manufacturing time and are often the culprit when a line needs to be shut down due to bottlenecks or processing delays. To think differently in today’s Good, Fast, and Cheap manufacturing environment we live in, everything must be on the table for review. Lean manufacturing is a commitment; you cannot rest on your loreals, because as soon as you do, your competition will present a better mousetrap.
When it comes to lean manufacturing and the idea of constant improvement there are only a few broad areas to look to for answers. You either need to add or replace equipment, introduce more technology, or change processes. It is hard to argue a case against new equipment if that’s what’s holding you back. Adding more technology on the other hand requires a lot more consideration. If you are swayed by marketing messages promising increased spindle time, increased uptime, decreased downtime, etc., you need to dive deeper. The real metric you should be considering is an overall increase in throughput, the bottom line on productivity. Often the promised benefits of new technology get lost in process or result in inefficiencies further down the line. Don’t kick the can down the line. Taking a good look at your processes is where the magic happens.
Process evaluation should precede virtually every investment throughout production, especially when it comes to materials, the lifeblood of any job. Materials sourcing, heat treating, flattening, squaring, deburring, cleaning, staging, and inventory control account for a considerable amount of time, and resources. Not to mention, the net outcome of materials prep can directly affect the overall quality and the potential for scrap. Consider the impact on your production line, and bottom line, if you could start a job with materials that arrive ready to go directly from receiving to machining.
Materials-Ready for Production
Materials Ready for Production (MRP) is real. TCI Precision Metals, a value-added materials distributor, developed the concept based on its precision Machine-Ready Blanks, which eliminate material prep, shorten setup time, reduce scrap, improve quality, and increase overall machining throughput by 25% or more.
Custom Machine-Ready Blanks are made to order, based on your unique specifications to make them ‘machine-ready.’ Typically, they are square, rectangular, or round stock milled to your custom net specifications. They can be produced as close as +/-.0005” dimensionally and as close as .002” in flatness, squareness, and parallelism. Machine-Ready Blanks eliminate the need for squaring up the material prior to finishing the part. Flatness is especially important as it reduces the tendency for part movement during the machining process, especially with large surface area parts.
By starting a production job with Machine-Ready Blanks you reduce the need for specialized machines or tying up machines that are better served performing other operations. Bottlenecks created by time-consuming setup and squaring operations are avoided, saving even more time. This increases shop capacity without adding overhead. Machine-Ready Blanks arrive pre-machined to specifications and are ready to go directly from your receiving dock onto your CNC machines. Machine-Ready Blanks are deburred, cleaned, and vacuum packaged to avoid damage during handling and shipping.
Thanks for reading -
Ben